* ALL INFORMATION IN THIS BUILD IS PROVIDED AS INFORMATION ONLY
I AM NOT RESPONSIBLE FOR HOW THIS INFORMATION IS USED AND ANY OPINIONS STATED ARE THAT OF THE AUTHOR.*Unless otherwise stated, all images and written content copyright of author. Any unauthorised reproduction, copying, duplication, plagiarism, scraping etc is strictly prohibited
Well got a Mightyboy a couple of months ago

(had a rattle you wouldn't believe

but was still running

) body is in good shape so put it on the car trailer and brought it home
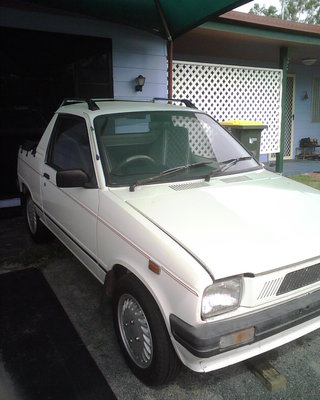
- Home
removed the motor
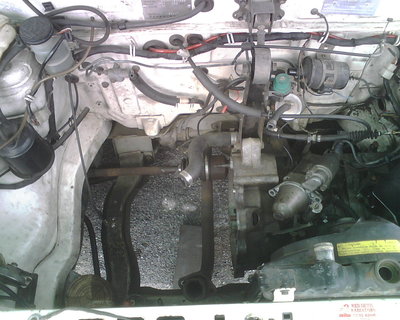
- no motor
and stripped it to find (no surprise) main bearings had failed
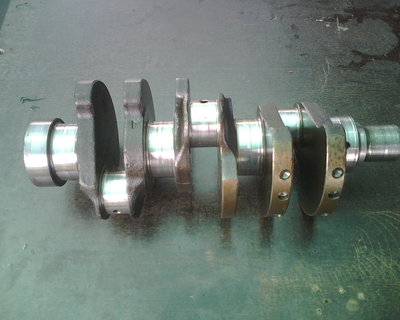
- crank
took the crank to work to check it and found the crank was bent,and main bearing area was damaged beyond grinding ...thanks to Billie a new-second hand crank was obtained. This crank was taken to work and polished and measured and came up good to go. The block was de-carbonised and given a light hone and assembly has begun crank has been refitted and oil clearances checked, pistons with new rings and big ends fitted and oil clearances checked (while many will feel this is not necessary -checking oil clearance - this will give a good indication of how good the machining was and which end of the oil clearance tolerance you are at which = expected life)
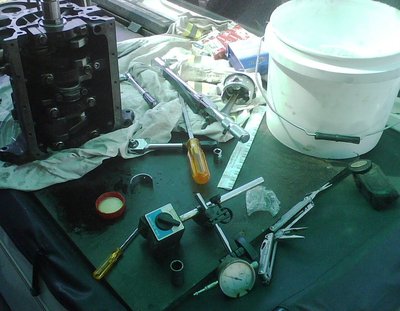
- piston/clearence
The oil pump was disassembled (had been apart before and one screw had the centre stripped out -someone used a standard screw driver to attempt to undo

)
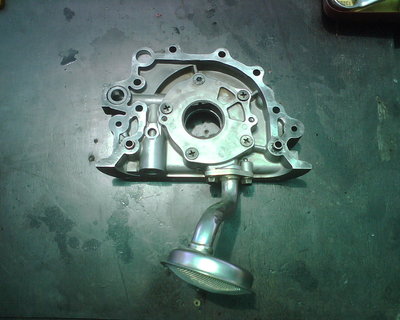
- oil pump
an impact driver was used to undo the other screws
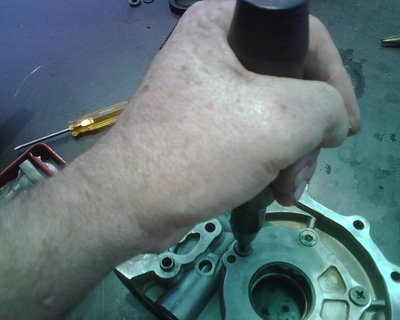
- impact driver
The screw with no centre was able to be undone using a cold chisel (failing this I would have drilled the head off the screw and this would have left enough of the screw protruding to be removed with vice grips/locking pliers) allowing the pump to be disassembled
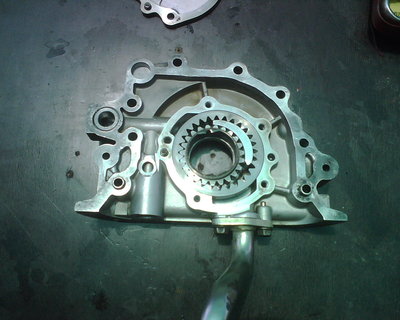
- oil pump apart
oil pump relief valve has been disassembled
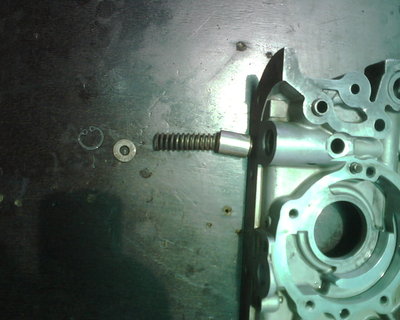
- oil relief
due to the age of the engine and the failed bearing's the housing has been built up and re-machined at work back to "as new" and reassembled using new screws:thumbup1: mainly cause I couldn't buy a new pump and the machining only cost my time.
O.K got a bit more time and refitted the oil pump/sump/inner timing cover then when fitting the rear water jacket cover ran into a little problem (snapped one of the bolts off

) so no worries I drilled the hole (dead centre) and thought I'd cheat (should'a know better) and attempt to use an "easy out" to remove the remains

- bolt

- easy out/tapered